In eateries worldwide, robots prepare meals, following precise instructions like they have for decades, but Ishika Singh aims to develop a robot capable of improvising in the kitchen, selecting ingredients, and crafting tasty dishes—a task too complex for current robot programming to handle due to its reliance on extensive kitchen knowledge, common sense, and adaptability.
Singh, a Ph.D. student in computer science at the University of Southern California, points out that roboticists typically rely on a classical planning approach, meticulously defining every action and its conditions, which proves insufficient when robots confront unforeseen circumstances. Crafting a comprehensive plan for a dinner-making robot requires not only cultural understanding but also knowledge of the specific kitchen setup, dietary preferences, and potential mishaps. Jesse Thomason, Singh's Ph.D. research supervisor, describes achieving this level of adaptability as a lofty ambition with transformative potential for various industries and everyday life.
Singh, a Ph.D. student in computer science at the University of Southern California, highlights the limitations of the classical planning approach used by roboticists, emphasizing the need for a more nuanced understanding of cultural contexts, kitchen configurations, dietary needs, and unexpected events in developing a dinner-making robot. Jesse Thomason, Singh's Ph.D. research supervisor, views attaining such adaptability as a significant aspiration that could revolutionize multiple industries and improve daily living standards.
While Language Models (LLMs) possess vast knowledge spanning various subjects, robots offer physical interaction capabilities lacking in LLMs. Integrating the two, as proposed in a 2022 paper, aims to leverage LLMs' knowledge with robots' ability to interact with the environment. Some see this collaboration as a means for robots to surpass preprogrammed limitations, sparking interest in teaching LLMs tool manipulation. However, concerns arise regarding LLMs' occasional errors, biased language, and privacy breaches. Despite their human-like qualities, skeptics question the wisdom of linking LLMs with robots due to their limitations and potential risks, such as generating false information and perpetuating stereotypes.
When ChatGPT debuted in late 2022, it sparked a revelation for engineers at Levatas, a West Palm Beach firm specializing in software for industrial site inspection robots, according to CEO Chris Nielsen. By integrating ChatGPT with Boston Dynamics, they developed a prototype robot dog capable of understanding and responding to spoken English commands, streamlining interactions for untrained workers. Nielsen emphasizes the importance of providing natural-language communication abilities to industrial employees, enabling them to instruct the robot effortlessly.
Levatas's LLM-enhanced robot demonstrates an understanding of language nuances and user intent. It can discern variations in commands, recognizing synonymous phrases and facilitating efficient communication between humans and machines. Instead of analyzing complex data spreadsheets, workers can simply inquire about specific readings from the robot's patrols.
While Levatas's proprietary software integrates various components, including speech-to-text transcription, ChatGPT, the robot itself, and text-to-speech capabilities, these technologies are now readily available commercially. However, the application of talking robot dogs in household settings remains distant, as Levatas's machine is optimized for industrial environments with specific tasks and limitations, unlike scenarios involving recreational activities or household chores.
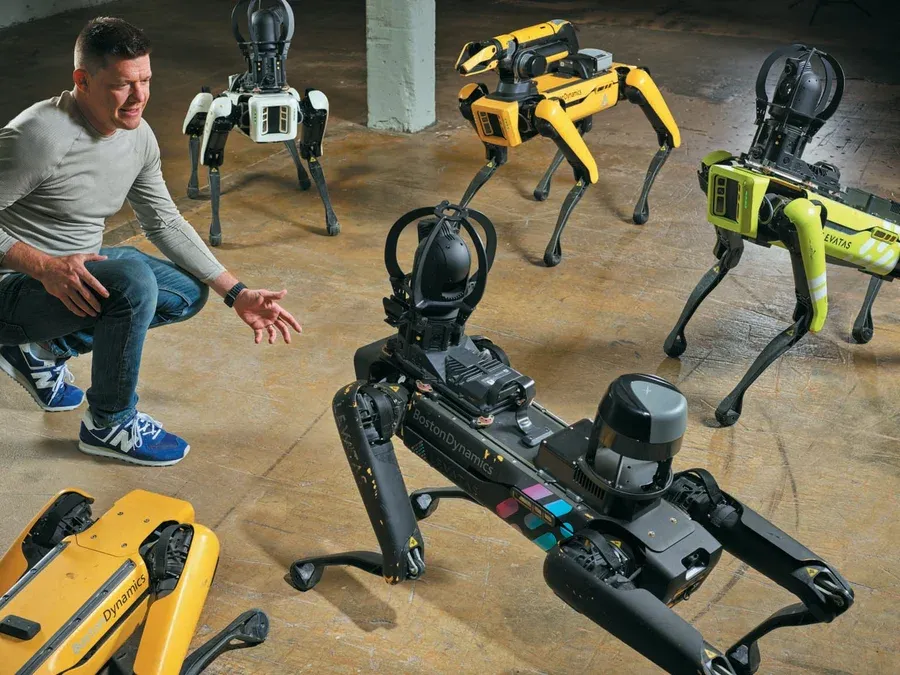
Regardless of its complexity, every robot operates within the constraints of limited sensors—such as cameras, radar, lidar, microphones, and detectors—linked to a set number of mechanical components like arms, legs, grippers, or wheels. These sensors feed data to the robot's computer, which processes information into binary code, representing electrical signals.
Utilizing its software, the robot assesses its available actions based on received instructions, selecting the most appropriate ones before translating them into electrical signals to initiate movement. It then evaluates its impact on the environment through sensor feedback, adapting its actions accordingly. This process is grounded in the physical realm, where metal, plastic, and electricity interact in real-world settings.
In contrast, machine learning operates in a conceptual space, employing neural networks composed of interconnected cells represented by binary code. Inspired by the structure of the human brain, each cell processes information received from numerous connections, assigning weights to inputs to determine whether to transmit signals. With more connections, the model generates more detailed outcomes, refining its performance by adjusting weights to approximate desired results—a process known as "machine learning."
Member discussion: